Shattering Glass: Unveiling the Hazards
Nickel Sulphide Inclusions in Glass and Canadian Regulations
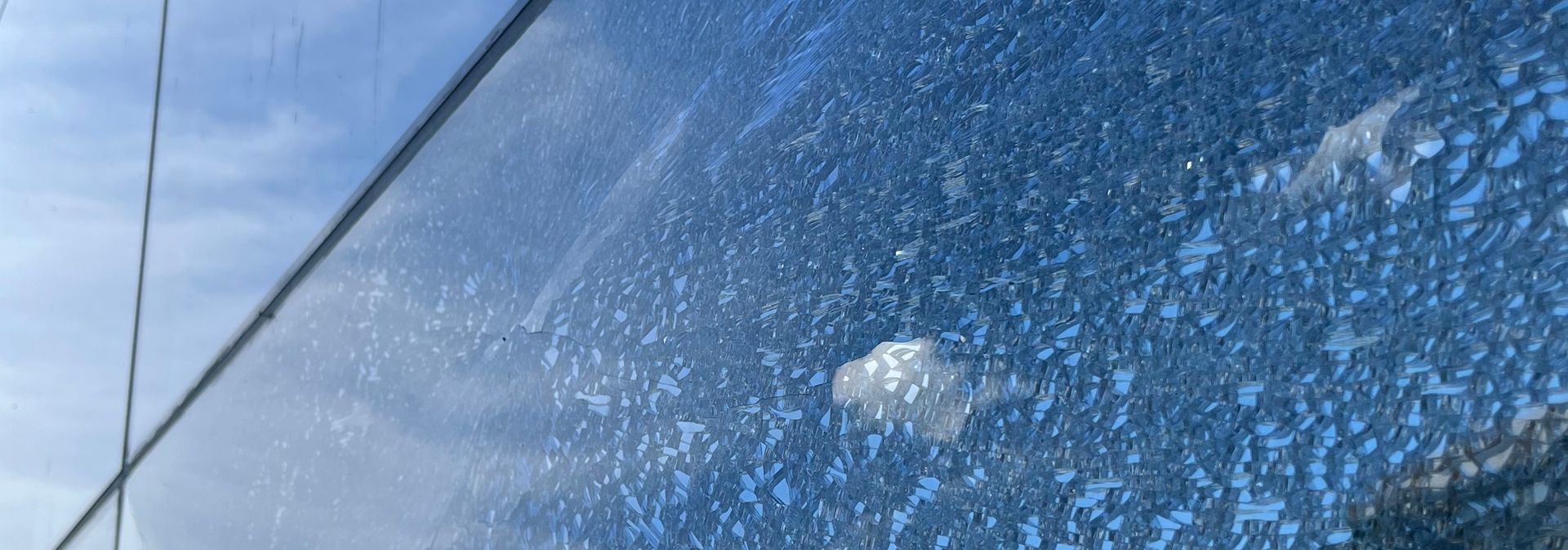
At Capacity Engineering, we conduct numerous forensic investigations concerning structural and building envelope issues across Canada. One of our Forensic Engagements was an investigation of a 55-Storey building where over 15 insulated glazing units (IGU’s) spontaneously shattered.
In situations like these, it is important to remind ourselves as our duty as a Professional; the Engineer shall regard the practitioner’s duty to protect the public welfare as paramount. As you can imagine, glass falling from 50+ storey’s of height poses a substantial risk to public welfare. When public safety is at risk, it is crucial that you work with the Authority Having Jurisdiction (AHJ) to ensure the necessary measures are taken to protect the public.
IGU’s or curtain wall assemblies serve multiple purposes and their design and installation are governed by the Ontario Building Code (OBC) as follows:
1. The design of the window to take environmental loads are governed under Part 4 of OBC 2012 “Structural Design”.
2. Additionally, windows (mainly curtain walls and window walls) at the edge of a buildings slab act as a guard rail and must resist guard loads where glass is located under the minimum height requirement. Thus, they are also governed under Supplementary Standard SB-13 “Glass in Guards”.
3. The window acts as an environmental separation and the design is also governed by Part 5 of OBC 2012 “Environmental Separations”. Part 5 also refers the designer to Part 4 of the OBC for environmental load calculations.
4. Additionally, the curtain wall is subject to testing under the North American Fenestration Standard/Specifications (NAFS) for Windows Doors and Skylights and meet the requirements of CSA A440S1. This testing is intended to ensure that the windows meet structural performance requirements as well as control of air leakage, condensation and rain penetration.
5. The installation of windows are governed by CSA A440.4 “Window Door and Skylight Installation”.
There are several factors that could cause glass in curtain walls to break. In some cases, it could even be a combination of several factors. Some factors include:
- Environmental loading - excessive wind loading.
- Axial shortening – columns shorten under axial load over time. If not properly considered, the shortening of the building can compress the curtain wall frames and shatter the glass.
- Thermal expansion – breakage due to excess temperature change and lack of expansion and contraction constraints.
- Installation issues – edges of glass being damaged.
- External Impact – sudden impact loading such as bird strike, debris, etc.
- Nickel Sulphide Inclusion – an impurity in the material that occurs during the manufacturing process.
While each of these factors can be explored, this forensic investigation concluded that the glass breakage was most likely due to the rare occurrence of Nickel Sulphide Inclusions.
What is Nickel Sulphide Inclusion (NiS)?
To properly understand NiS, it is important to understand the process of manufacturing tempered glass. Tempered glass is a product from annealed glass (or sheet glass) formed by process of heating and cooling.
The glass is heated to a temperature of around 600°C then it rapidly undergoes a high-pressure cooling procedure called “quenching”. During this process, high-pressure air, blasts the surface of the glass to cool the outer surfaces at a much quicker rate than the center. As the center of the glass cools, it tries to pull back from the already cooled outer surface. This causes the center to remain in tension with the outer surfaces having a counterbalancing compression stress which is what gives the strength to tempered glass.
After tempered glass is formed, the stress profile through the thickness of the glass becomes parabolic as seen in Figure 1 below.
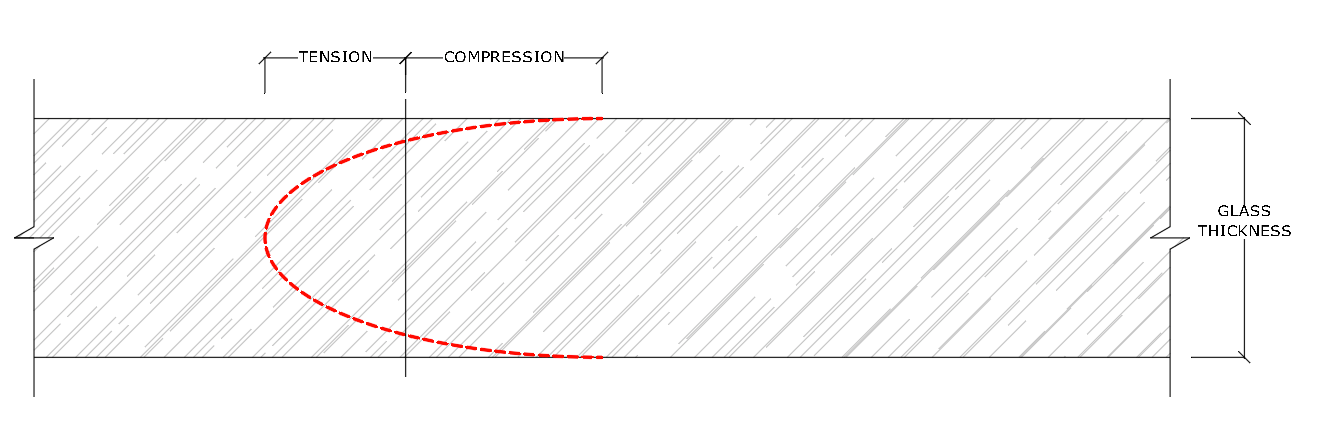
However, during the process of manufacturing the annealed glass, there is a possibility that a nickel sulphide stone forms in the tension zone due to nickel contamination. These stones can vary in size from 0.05mm to 0.1mm.
When the tempered glass is later exposed to varying temperatures in the field, the inclusion changes in size and can grow to a size to that causes enough additional internal tensile stress to exceed the counterbalancing compression stresses and shatter the glass. This has the highest risk of occurrence in the first 10 years of the tempered glass life.
The shattering of the glass creates an extremely loud shattering noise and breaks almost instantaneously into thousands of tiny pieces.
How to determine a NiS Failure?
Now while you may be wondering how to determine if a glass shattered due to Nickel Sulphide Inclusion, the reality is that there is one main tell tail: The Butterfly Effect.
In Chaos Theory, the Butterfly Effect is the phenomenon that the world is interconnected such that one small occurrence can cause major consequences in a much larger, complex system. In the office, we refer to this as St. Venants Principle: the principle of local vs. global. The principle that one must consider the local aspects of a structure as well as the global. A local failure could also cause a catastrophic global failure.
With respect NiS failure, The Butterfly Effect occurs on a much smaller scale as described in Chaos Theory. A small (0.05mm-0.1mm) NiS inclusion can cause an entire failure of the IGU on a much larger scale; and ironically, the origin of the glass failure resembles a butterfly. The NiS inclusion fracture origin starts with a single small line which then branches on each side and continues to branch in a chaotic manner. The Figure below show examples of the “butterfly” resembling fracture origin due to nickel sulphide inclusion.
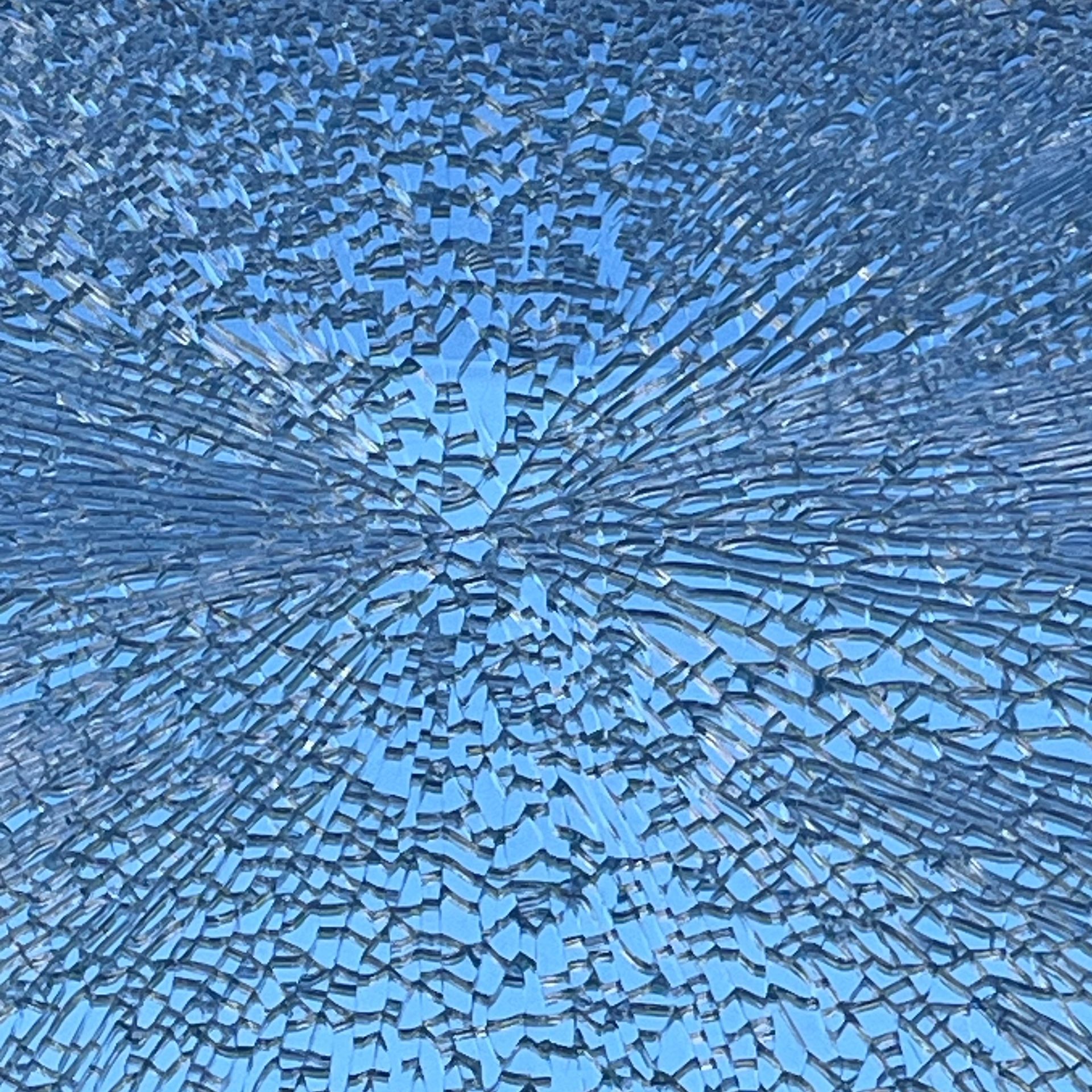
This butterfly crack is a unique shatter pattern and typically the presence of this crack origin gives the engineer or manufacturer strong evidence on the cause. However, it is best practice to have the NiS inclusion verified in a laboratory. But the reality is that it is almost impossible to visually identity NiS inclusions in the manufacturing process.
How do we prevent this issue?
The main and most common method of reducing risk of NiS breakage is heat soak testing. Heat soak testing is destructive testing where you heat the tempered glass in a chamber at approximately 200°C - 300°C. This test accelerates the growth of the NiS inclusion in attempt to purposely shatter the glass with the NiS inclusion. This test is expensive but has been proven to significantly reduce the risk of NiS induced breakages in the field.
Currently there is no North American standard for heat soak testing, however, industry best practice and SB-13 requirements are to perform the heat soak test to the European Standard EN 14179-1.
How does our Code address this issue?
The frank reality is that prior to the 2012 Ontario Building Code, buildings in Ontario were allowed to have only tempered glass IGU’s. However, this changed after several high-profile failures from 2010-2012 in Toronto caused the Ministry of Municipal Affairs and Housing (MMAH) to discuss methods of reducing the risk of NiS breakages were discussed. The MMAH then released Supplementary Standard SB-13 of the Ontario Building Code.
The objective of SB-13 is to provide requirements for the design and construction of glass in guards and reduce the probability of breakage of glass panels and injury to persons in the vicinity of a building as a result of failing broken glass.
The requirements of SB-13 is now listed in Table 2.1.1.1. attached below:
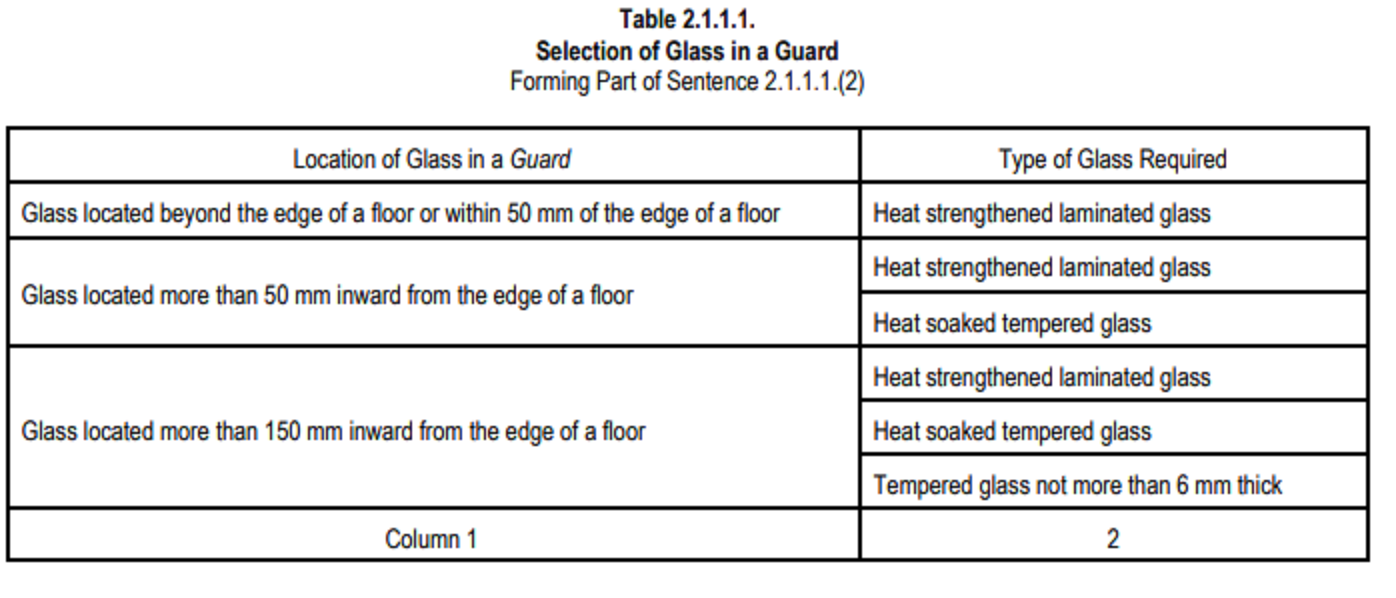
This table under SB-13 provides requirements in Ontario that all glass near the edge of a buildings slab be heat strengthened laminated or heat soaked tempered.
CEL was involved in the forensic investigation of the high-profile failures in Toronto which caused MMAH to develop this supplementary standard. The reality is at the time of construction, the tempered IGU panels met all Ontario Building Code requirements and formed the basis of SB-13 requirements to less commonly allow tempered glass.
IGU’s and curtain walls are generally an evolving area of professional practice for Engineers and Architects and as research develops so does our Code. The Codes main objective as set out in Division A, Part 2, is to limit the probability that as a result of design or construction, a person in or adjacent to the building will be exposed to unacceptable risk or hazards. We, as Professionals, must continue to advance the profession with our knowledge and expertise to further protect public safety.
CEL’s President, Maurice Quinn P.Eng., currently sits as the Chair of the Fenestration Canada Technical Sub-Committee on failure determination of fenestrations. CEL is working closely with Fenestration Canada to improve our standards based on the work CEL has been conducting across Canada.
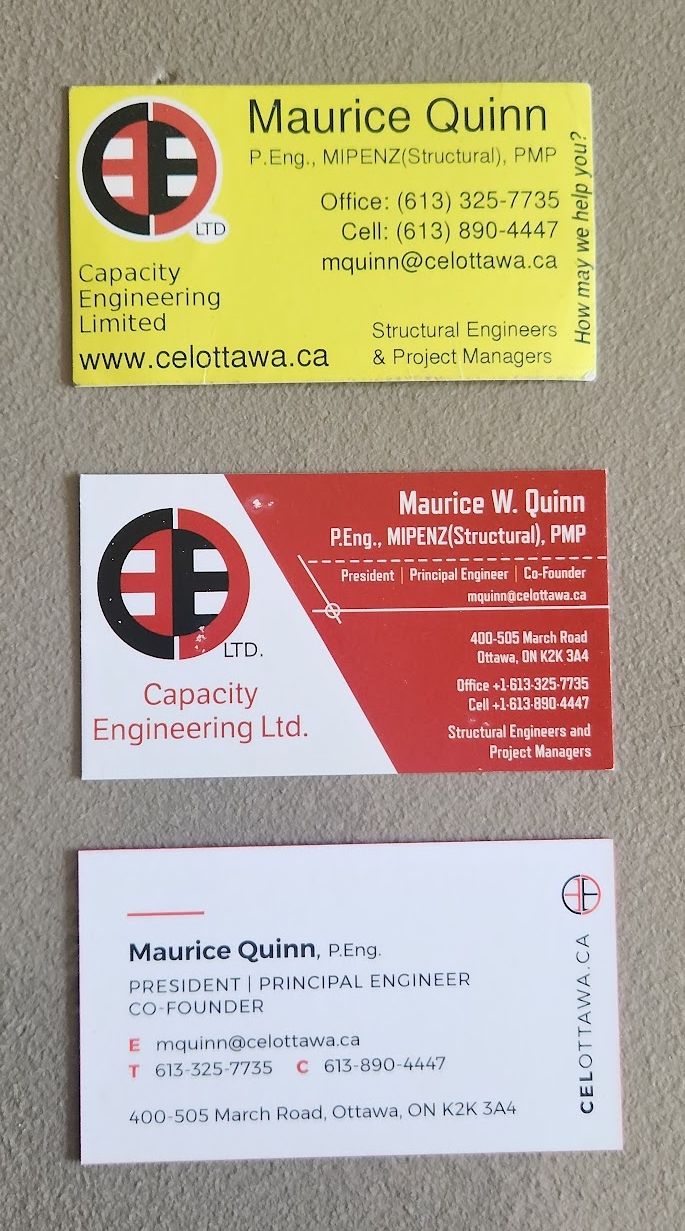