Shop Drawings, Seismic Systems, and the Construction Process – The importance of detailing and reviews
Shop Drawings, Seismic Systems, and the Construction Process – The importance of detailing and reviews
Really? October, and suddenly we have a new Blog post? Must be the end of the busy season… Unfortunately, like weather, there is a distinct seasonality to Structural Engineering in Canada
I digress; today’s post is about detailing and shop drawing procedure.
Let’s use a seismic system as an example. These are designed by the Engineer of Record (EOR), often subject to component design (such as the connections for a steel frame), and ubiquitous. Every building has a lateral load resisting system, whether this is primarily to address wind loads, or designed to handle both wind and seismic separately, each building has some way of handling the loads that push on our buildings from the side, or “laterally”. These are the Lateral Loads Resisting Systems (LLRS) of buildings, and they come in many forms. Sometimes they are as simple as timber framing with a steel strap or let in brace running diagonally down the wall, as easy as fastening on a sheathing system (timber or gyprock are both possible, and often mixed), or as complicated as tuned mass dampers and energy dissipating devices. All buildings are constructed with an LLRS of some kind.
So what happens when loads travel where they don’t belong, or where the Engineer of Record (EOR) didn’t intend for them to go? Well, quite possibly nothing, but also quite possibly this may have disasterous consequences. Every building should have a discrete, reliable, well constructed and maintained LLRS handling the lateral loads. This starts with the design process, but must be cared for throughout construction and in service. Everything from the way in which the staircases are constructed and installed within the building through to the running of mechanical pipes and the installation of drywall, indeed even the delivery of some furniture, may have a serious impact on the LLRS during construction or thereafter.
So what do we do? How do we ensure that the EOR’s design intent is reflected in what is constructed? Well, this is the role of Shop Drawings; the intent of others designing components for the building is to be shown on a set of engineering drawings created for those components, simply termed “Shop Drawings” as they are the drawings for components being produced in a fabrication shop. Seems simple, but a great deal of things can go wrong.
Many disasters may be traced back to mistakes made during the shop drawings process. The Kansas City Hyatt skywalk collapse comes to mind immediately. As an EOR, we have no choice but to review the work of anyone providing components to our project, and ensure that appear to be based on an understanding of our structure’s requirements and are likely to meet the intent of our design. We aren’t perfect, and everyone makes mistakes, but by working together in a clear and open process, mistakes are minimized, and many lives of unsuspecting members of the public are saved.
So what makes for a good shop drawing process? Well, this is founded upon everyone taking their role seriously and ensuring that those areas of work they are responsible to undertake and review are covered off properly. While this differs somewhat in various jurisdictions, generally they follow a regimented process. In Canada that looks like this:
1. The component designers use the project’s drawings and specifications to come up with their design. They represent these on Shop Drawings (SD) they produce.
2. The Constructor reviews the SDs, paying special attention to field measurements and constructability. They apply their SD approval seal and send them to the Architect.
3. The Architect confirms that the SDs will produce work which meets the intent of their design, for aesthetics (form), function, durability, and generally match their intended size and massing (dimensions check). They apply a review seal (not relieving the Constructor of their obligation to meet the requirements of the D&S), and send these to the respective Engineer (by discipline for each component type).
4. The Engineer (for structural elements, the EOR) reviews the SDs for compliance with the intent of the design, and seals them as being reviewed.
For all parties, these reviews come in flavours:
i. Reviewed [ie: Looks good and complies with my needs.]
ii. Reviewed as Noted [ie. I made a few, typically minor, annotations; document complies with my needs so long as these are incorporated.]
iii. Revise and Resubmit [ie: Please try again.]
iv. Reviewed in Part [NB: Generally a partial comes with explanations.]
v. Not Reviewed [NB: This time I would say the lack of review is invalid without explanation.]
Turn Around Time: Ah, the magic of everyone wanting their answers yesterday. While these vary by contract, generally speaking people are afforded between three and seven working days to complete their reviews. Erroneous, incomplete, or otherwise problematic SDs can have massively negative impact on projects. They are important and serious documents which are frequently afforded too little attention in construction practice.
That’s it; while it seems simple and straight-forward, a careful attention to detail (pun intended) is required. In our practice, we try to make sure that the Shop Drawings are reviewed by at least two people, following again our Second Set of Eyes (SSoE) procedure to further safeguard both life and property. Even with a robust SSoE procedure, errors and omissions can escape the attention of even the best team.
If you remember but one thing from today’s post, let it be this: In absence of an SSoE system, you’re flying blind, and your paper airplane is going to be taken down by little more than the ink on the page… Because for our ink, the consequences of error are girded by steel and written in stone.
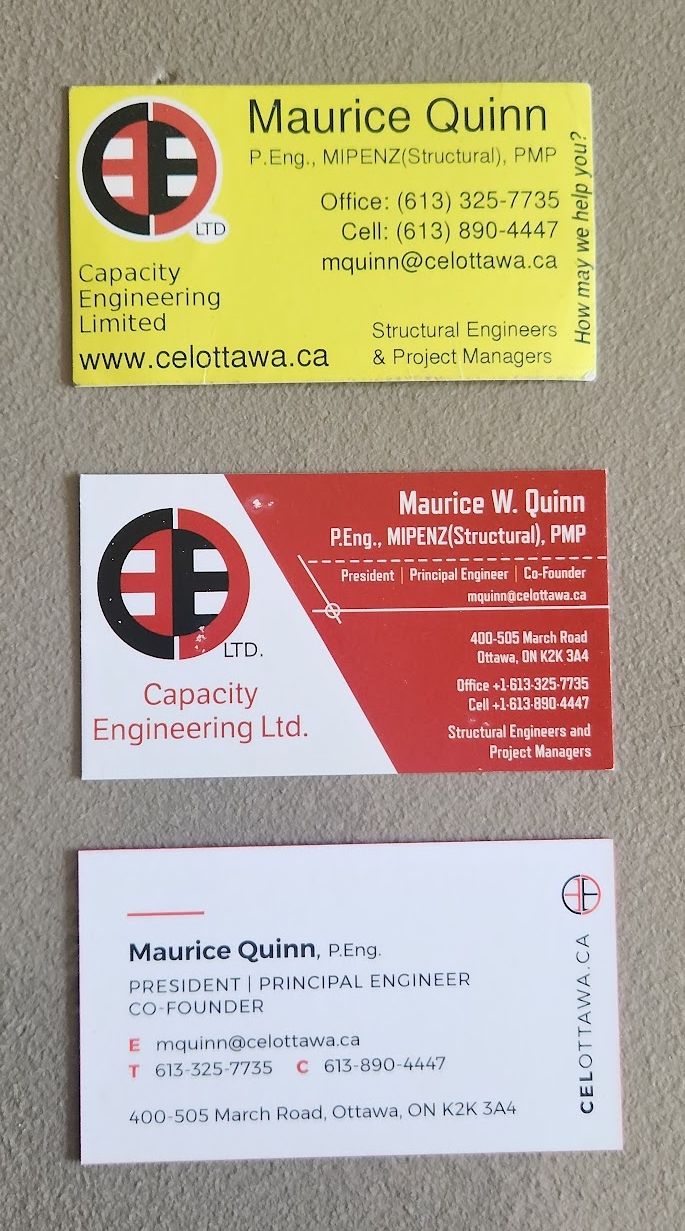